Why Do We Love Polymer Magazines?
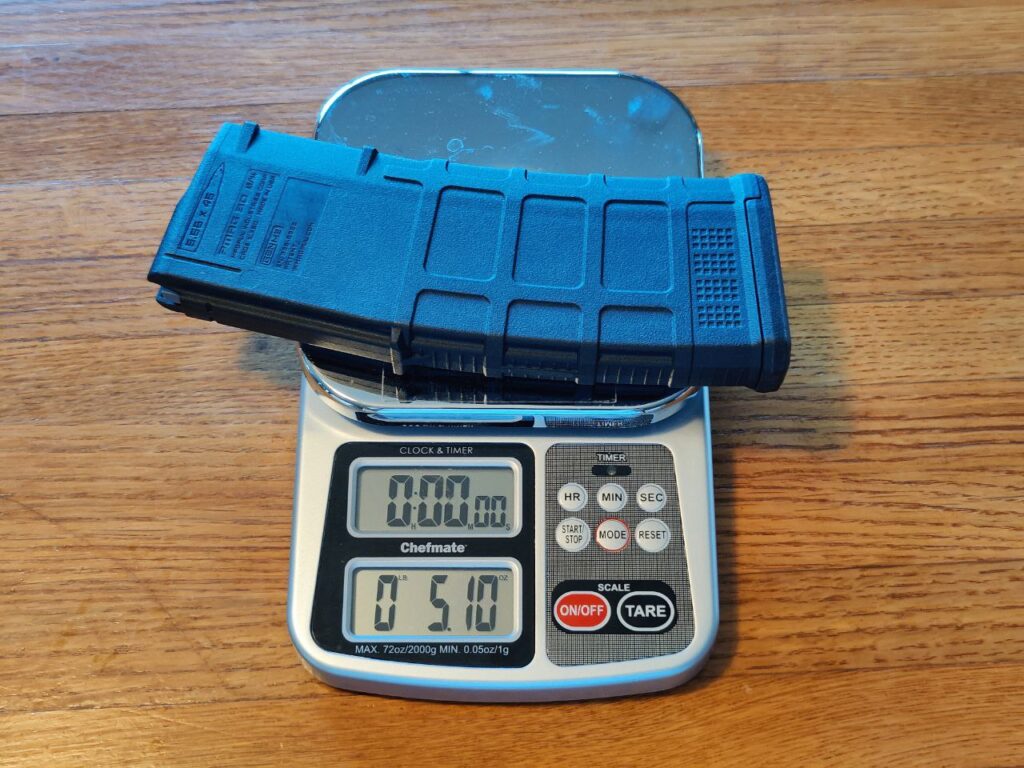
The magazine is one of the most critical components of any repeating firearm. It must reliably handle cartridges with a variety of different bullet designs, present them high enough for the bolt to pick them up without letting them escape prematurely, and maintain the exact same feed angle from the first round to the last. A 99.9% reliability rate is considered hopelessly poor. Detachable magazines are especially challenging to engineer, as they must achieve the same level of reliability while being lightweight, simple, and inexpensive enough to be treated as consumable if not outright disposable.
The above being the case, from the time James Paris Lee invented the box magazine in the 1870s through about two decades ago, detachable magazines were almost exclusively constructed of metal. Now, it’s relatively uncommon to see a new bolt-action or semi-automatic rifle that doesn’t at least have polymer magazines available for it, if it doesn’t come with one already. Plastics are nothing new, so why is it that they didn’t become the dominant material for firearm magazines until relatively recently? Moreover, why has polymer mostly supplanted steel and aluminum as the material of choice for rifle magazines, but not in pistols?
Why Metal?
Until the 1960s, detachable magazines for centerfire firearms were almost always made of stamped pieces of sheet steel, which were then folded over and welded to create a magazine body. Separate stampings produced a follower and a floorplate; the only component not made of pressed steel was the spring. Stamping and spot-welding sheet metal was the cheapest way to mass-manufacture items that needed to be strong and durable yet (relatively) lightweight. Steel was the obvious choice due to its strength and low cost.
It wasn’t until the AR-15 was developed in the late 1950s and early 1960s that aluminum magazines began to become widespread. ArmaLite chose aluminum not for any engineering reason, but because it is much lighter than steel, and was by that point cheaper and easier to work with. Early M16 magazines were intended to be basically disposable, so little consideration was made for long-term durability, which in turn is why the original 20-rounders were made out of such thin and flimsy material. When Colt engineers developed the 30-round M16 magazine we all know today, they worked to make it more durable and reliable than its straight-walled 20-round predecessor, but they could only do so much given the inherent limitations of the material and the size constraints of the receiver’s internal geometry.
Magpul didn’t develop the first fully polymer magazine, or even the first fully polymer magazine for the AR platform, but their PMAG was the first magazine for that platform to be sufficiently reliable and durable for military use. Once Magpul cracked the code, two things happened: they adapted the same technology to other platforms, and other companies adapted the same technology to develop their own magazines.
Feed Lip Deformation
It appears that the main driver of interest in fully polymer magazines for the AR platform was reliability. Aluminum M16/M4 magazines were always notorious for two main failure modes: follower jams and misfeeds caused by bent feed lips. The former problem was relatively easy to solve: simply replace the followers in old magazines with taller anti-tilt versions. The latter was much more challenging. Given the level of precision with which a magazine must feed cartridges into a firearm’s action, feed lips damaged through repeated use and abuse can warp just enough to impair reliability without being visibly bent. In short, it’s an invisible failure mode, and even the best aluminum AR magazines’ thin construction leaves them very prone to it.
There are basically two fixes to the feed lip deformation problem, both requiring a change in material. Making the magazine out of steel doesn’t entirely prevent the feed lips from bending, but it does make it very difficult for that to happen, and steel magazines can easily be made to similar dimensions and using the same manufacturing techniques as their aluminum counterparts. The other fix is to make magazines entirely out of a polymer material, which doesn’t bend the same way. Common steels and aluminum alloys are subject to plastic deformation, which means they can bend into a new shape. Imagine dropping a clay ball on a tile floor—when you pick it up, the bottom will be flattened out. Polymer, on the other hand, tends to experience elastic deformation under the types of mechanical stresses magazines experience. This means they still bend, but spring back into their original shape when the force is removed, like a rubber ball. High-speed video shows that polymer magazines can bend quite a lot when dropped or driven over with a truck, but they always spring back into shape unless the force is sufficient to start a crack. Even a cracked polymer magazine may still feed if the crack is small enough and in a non-critical location, such that the magazine body still retains the correct shape.
What allowed Magpul to succeed in 2007 where Thermold and others had previously failed was their use of a different polymer composition. A plastic component generally needs to be thicker than a metal one to achieve the requisite level of structural strength, but the tight constraints of the AR-15 receiver made that task difficult. The use of just the right proprietary polymer reinforced with enough fiberglass makes PMAGs stiffer but less brittle and more heat-resistant than their predecessors, while still fitting in the gun.
Weight
Contrary to popular belief, polymer AR magazines are not lighter than their aluminum “GI” Colt-pattern counterparts, but they aren’t more than about an ounce heavier at the worst. They are, however, much lighter than steel equivalents. The weight advantage is so significant that the USSR developed polymer magazines for the AKM and AK-74 families all the way back in the late 1960s after experiments with aluminum magazines apparently failed. The Izhevsk-developed AG-4S magazine is made of a fiberglass-reinforced phenol-formaldehyde resin often incorrectly referred to as Bakelite, epoxied around a steel subframe with locking lugs to mate up to the rifles’ steel receivers. Because the AK was designed around a much thicker slab-sided steel magazine, more space was available internally for thick polymer feed lips, making the polymer magazines easier to engineer.
Lancer Systems takes a similar approach with their A5 and A7 Advanced Warfighter Magazines in 5.56 and 7.62, respectively. They use a thinner and weaker translucent plastic than Magpul’s composition to form the magazine body, which is molded around a steel “collar” incorporating just the feed lips. That way, steel is only used in the areas which need to be the strongest, while weight is minimized throughout.
To show the weight difference between different types of AR-15 magazine, I weighed a few examples from my collection. I didn’t have access to an aluminum GI mag, but for reference, they’re said to weigh between 3.95 and 4.1 ounces. Note that the Korean-made steel magazine weighs about twice as much as an aluminum one, and about 60% more than a Gen 3 PMAG.
Cost
Irrespective of any reliability or weight advantages, perhaps the biggest reason why plastic is the holy grail of magazine materials is that it’s so cheap to work with. Metal stamping was the preferred low-cost manufacturing method in the middle of the last century, but we live in the future, so injection molding has supplanted it. A set of molds costs hundreds of thousands of dollars, but the marginal cost—the cost to make each additional part—is in the neighborhood of cents or a few dollars at most. To mold an entire magazine body takes less than a minute. This means that polymer magazines can be turned out in huge numbers at extremely low prices with a high level of consistency. Even in ban states such as California, 10-round polymer magazines are still cheaper than aluminum and steel equivalents.
Why Not Plastic?
If polymer magazines are so great, then why are they ubiquitous in rifles but relatively uncommon in pistols? Mainly because pistols impose the same dimensional constraints that made it take so long to develop a reliable polymer magazine for the AR platform, but with one major notable exception. Glock magazines are made more or less the same way as Lancer mags. Whereas most pistols use conventional stamped steel technology, Glock opted to injection-mold a plastic shell around a steel subframe. As plastics were already their bailiwick, this process was familiar to them, allowing them to make pistols and magazines on the cheap. The only real disadvantage is that a wider magazine necessitates a wider pistol frame, contributing to that notorious blocky feel in the hand.
Conclusion
This is one of the longest single posts I’ve ever written for the SDCGO blog, so I’ll cut it off here before too many of you fall asleep. Did you notice that one of the PMAGs in the photos above is actually an EMAG? In a future blog post, I’ll explain what the EMAG was and why it needed to exist, as well as some of the less-well-known peculiarities of the Magpul PMAG family.